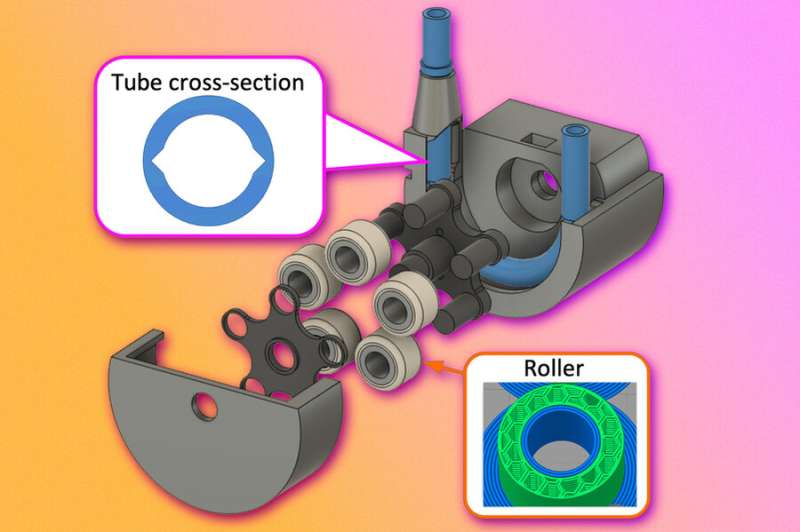
Mass spectrometers are extremely precise chemical analyzers that have many applications, from evaluating the safety of drinking water to detecting toxins in a patient’s blood. But building an inexpensive, portable mass spectrometer that could be deployed in remote locations remains a challenge, partly due to the difficulty of miniaturizing the vacuum pump it needs to operate at a low cost.
MIT researchers utilized additive manufacturing to take a major step toward solving this problem. They 3D printed a miniature version of a type of vacuum pump, known as a peristaltic pump, that is about the size of a human fist.
Their pump can create and maintain a vacuum that has an order of magnitude lower pressure than a so-called dry, rough pump, which doesn’t require liquid to create a vacuum and can operate at atmospheric pressure. The researchers’ unique design, which can be printed in one pass on a multimaterial 3D printer, prevents fluid or gas from leaking while minimizing heat from friction during the pumping process. This increases the lifetime of the device.
This pump could be incorporated into a portable mass spectrometer used to monitor soil contamination in isolated parts of the world, for instance. The device could also be ideal for use in geological survey equipment bound for Mars, since it would be cheaper to launch the lightweight pump into space.
“We are talking about very inexpensive hardware that is also very capable,” says Luis Fernando Velásquez-García, a principal scientist in MIT’s Microsystems Technology Laboratories (MTL) and senior author of a paper describing the new pump.
“With mass spectrometers, the 500-pound gorilla in the room has always been the issue of pumps. What we have shown here is groundbreaking, but it is only possible because it is 3D-printed. If we wanted to do this the standard way, we wouldn’t have been anywhere close.”
Velásquez-García is joined on the paper by lead author Han-Joo Lee, a former MIT postdoc; and Jorge Cañada Pérez-Sala, an electrical engineering and computer science graduate student. The paper is published today, April 25, in Additive Manufacturing.
Pump problems
As a sample is pumped through a mass spectrometer, it is stripped of electrons to turn its atoms into ions. An electromagnetic field manipulates these ions in a vacuum so their masses can be determined. This information can be used to precisely identify the constituents of the sample. Maintaining the vacuum is key because, if the ions collide with gas molecules from the air, their dynamics will change, reducing the specificity of the analytical process and increasing its false positives.
Peristaltic pumps are commonly used to move liquids or gases that would contaminate the pump’s components, such as reactive chemicals. They are also used to pump fluids that need to be kept clean, like blood. The substance being pumped is entirely contained within a flexible tube that is looped around a set of rollers. The rollers squeeze the tube against its housing as they rotate. The pinched parts of the tube expand in the wake of the rollers, creating a vacuum that draws the liquid or gas through the tube.
While these pumps do create a vacuum, design problems have limited their use in mass spectrometers. The tube material redistributes when force is applied by the rollers, leading to gaps that cause leaks. This problem can be overcome by operating the pump rapidly, forcing the fluid through faster than it can leak out. But this causes excessive heat that damages the pump, and the gaps remain. To fully seal the tube and create the vacuum needed for a mass spectrometer, the mechanism must exert additional force to squeeze the bulged areas, causing more damage, explains Velásquez-García.
An additive solution
He and his team rethought the peristaltic pump design from the bottom up, looking for ways they could use additive manufacturing to make improvements. First, by using a multimaterial 3D printer, they were able to make the flexible tube out of a special type of hyperelastic material that can withstand a huge amount of deformation.
Then, through an iterative design process, they determined that adding notches to the walls of the tube would reduce the stress on the material when squeezed. With notches, the tube material does not need to redistribute to counteract the force from the rollers.
The manufacturing precision afforded by 3D printing enabled the researchers to produce the exact notch size needed to eliminate the gaps. They were also able to vary the tube’s thickness so the walls are stronger in areas where connectors attach, further reducing stress on the material.
Using a multimaterial 3D printer, they printed the entire tube in one pass, which is important since postassembly can introduce defects that can cause leaks. To do this, they had to find a way to print the narrow, flexible tube vertically while preventing it from wobbling during the process. In the end, they created a lightweight structure that stabilizes the tube during printing but can be easily peeled off later without damaging the device.
“One of the key advantages of using 3D printing is that it allows us to aggressively prototype. If you do this work in a clean room, where a lot of these miniaturized pumps are made, it takes a lot of time and a lot of money. If you want to make a change, you have to start the entire process over. In this case, we can print our pump in a matter of hours, and every time it can be a new design,” Velásquez-García says.
Portable, yet performant
When they tested their final design, the researchers found that it was able to create a vacuum that had an order of magnitude lower pressure than state-of-the-art diaphragm pumps. Lower pressure yields a higher-quality vacuum. To reach that same vacuum with standard diaphragm pumps, one would need to connect three in a series, Velásquez-García says.
The pump reached a maximum temperature of 50°C, half that of state-of-the-art pumps used in other studies, and only required half as much force to fully seal the tube.
“Fluid movement is a huge challenge when trying to make small and portable equipment, and this work elegantly exploits the advantages of multimaterial 3D printing to create a highly integrated and functional pump to create a vacuum for gas control. Not only is the pump smaller than pretty much anything similar, but it generates vacuum 100 times lower as well,” says Michael Breadmore, professor in analytical chemistry at the University of Tasmania, who was not involved with this work. “This design is only possible by the use of 3D printers and nicely demonstrates the power of being able to design and create in 3D.”
In the future, the researchers plan to explore ways to further reduce the maximum temperature, which would enable the tube to actuate faster, creating a better vacuum and increasing the flow rate. They are also working to 3D print an entire miniaturized mass spectrometer. As they develop that device, they will continue fine-tuning the specifications of the peristaltic pump.
“Some people think that when you 3D print something there must be some kind of tradeoff. But here our group has shown that is not the case. It really is a new paradigm. Additive manufacturing is not going to solve all the problems of the world, but it is a solution that has real legs,” Velásquez-García says.
More information:
Han-Joo Lee et al, Compact peristaltic vacuum pumps via multi-material extrusion, Additive Manufacturing (2023). DOI: 10.1016/j.addma.2023.103511
This story is republished courtesy of MIT News (web.mit.edu/newsoffice/), a popular site that covers news about MIT research, innovation and teaching.
Citation:
Researchers 3D print a miniature vacuum pump (2023, April 25)
retrieved 25 April 2023
from https://techxplore.com/news/2023-04-3d-miniature-vacuum.html
This document is subject to copyright. Apart from any fair dealing for the purpose of private study or research, no
part may be reproduced without the written permission. The content is provided for information purposes only.
Stay connected with us on social media platform for instant update click here to join our Twitter, & Facebook
We are now on Telegram. Click here to join our channel (@TechiUpdate) and stay updated with the latest Technology headlines.
For all the latest Technology News Click Here